High-intensive Mixers
Superior mixing with one-step mix-granulating for a wide range of applications and materials
Solutions and Features
Get More Uniformity with Counter-Current Mixing
Our proprietary counter-current mixing technology is the most effective mixing technique for consistent uniformity, homogeneity, and rapid mix time. This multi-tool mixing technology consists of a rotating pan, high-speed rotor, and plow that works with a variety of materials, from powders to slurries to high-viscosity mixes, and allows for:
- Homogenizing / Granulating / Densifying – all in one machine
- Faster Mixing
- Repeatable batches
- Independently controlled mixing tools for custom mix designs
Granulate or Pelletize with a Single Machine
Lancaster Products high-intensity K-series mixers use a counter-current rotating pan and high-energy rotor to rapidly mix and pelletize or granulate in a single machine in a single operation.
- Reduce the need for multiple pieces of mixing and pelletizing equipment. Our high shear mixers can do both in a single operation.
- Higher on-size yields compared to traditional mixing and pelletizing equipment.
- K-series mixers are the ideal solution to mix and granulate bulk material for various industries including building materials, ceramics, fertilizers, and more.
Achieve Batch Precision with Steady-State Throughput
The Lancaster Products Continuous Batch Processing (CBP) System design offers the accuracy, consistency, and higher yields of batch processing with high production rates of a continuous line.
- Get the benefits of both continuous and batch processing
- Consistent throughput
- increase mix quality and productivity
- Can be designed with multiple mixers to double output capabilities
- Parallel lines create redundancy for a continuous output
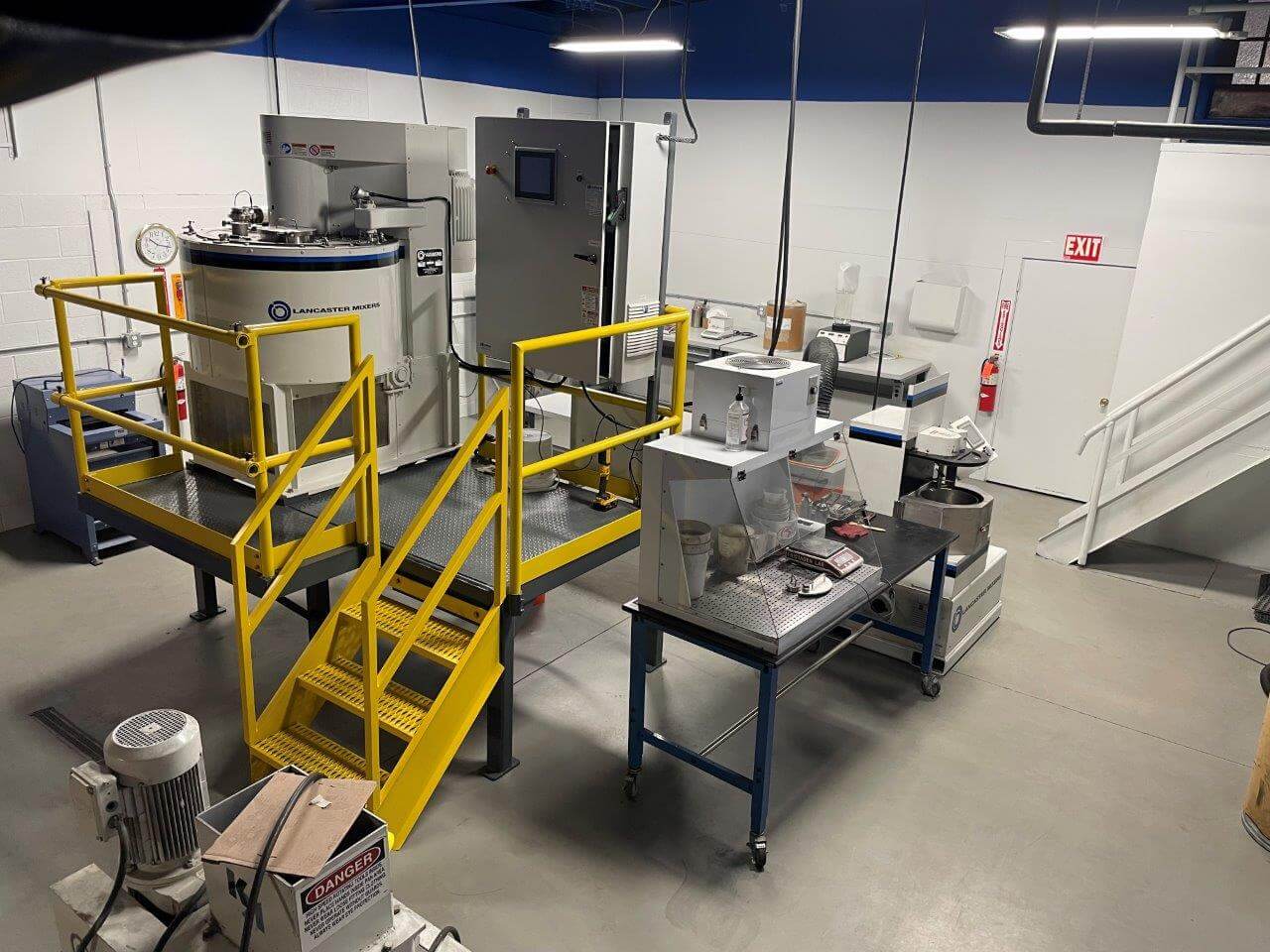
The Lancaster Products Difference
Lancaster Products is committed to providing the highest quality products and customer service. As your partner in material mixing, you can count on us to deliver:
- Quick response times to your inquiries
- Customer-focused solutions – we take the time to understand your product & process requirements
- Continued support for process optimizations or to scale solutions as your needs evolve
- Onsite test lab with dedicated applications engineers to support process & product development
- Decades of mixing experience with a variety of materials/across various industries
Our Latest News and Blog
Achieving Homogeneous Mixtures from Extremely Different Materials in a Lancaster Mixer
The process of achieving homogeneous mixes from extremely different materials can pose a significant challenge in various industries. However, with advancements in mixing technologies, one notable solution is the counter-current mixing action of the Lancaster...
In-House Process Lab Renovations Augment Dedication to Mix Design Optimization
At Lancaster Products, we’ve been busy renovating our in-house materials processing laboratory, literally from floor to ceiling. Equipment upgrades and the addition of a production-sized mixer were implemented to provide customers with a more complete and accurate...
Save Time & Increase Yields by Mixing & Granulating in One Machine
After more than 75 years in business and hundreds of installations worldwide, we still get excited when we demonstrate Lancaster Mixers ability for homogenous powder mixing and granulating in a single batch operation. With an average batch runtime under ten minutes...
