Glass
Lancaster Products High Shear Mixers are used for the batch preparation of various types of glass, such as sheet glass, bottle glass, automotive glass, artisan’s glass, and the high-precision, flat panel glass used in the majority of the world’s LCD and LED thin glass applications.
The Lancaster Mixer produces granulation of the raw glass batch materials. Granulation of the raw materials can result in reduced melting times in the furnace and an overall reduction of the energy required to melt the raw materials in the glass furnace. Granulation of raw materials can also reduce any demixing problems.
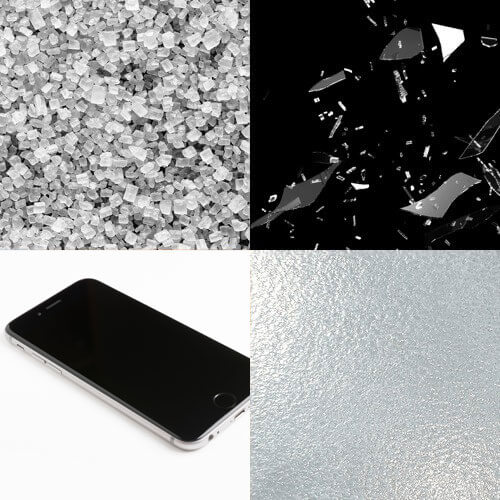
Advantages of Lancaster High Shear Mixers In The Glass Industry:
- Reduced mixing times
- Higher homogeneity of the end mixture
- Reduction in energy required from the melting furnace
- Reduced iron contamination due to the reduced wear in the mixer because of the rotating mixing pan used to transport the material into the mixing tool
- Consistent mixing of all raw materials, even when they have different densities, particle sizes and grain shapes
GLASS MANUFACTURING
A cleaner glass batch preparation process can be produced with the Lancaster Mixer. Reduction of dust and easier handling and transport of the material is accomplished by mixing and blending the glass batch with water in the Lancaster Mixer prior to the introduction to the furnaces.
Lancaster Products Roll Crushers are used extensively by glass manufacturers to reduce recycled glass prior to reintroduction into the furnace. Our double roll crushers are designed to reduce, in a single pass, material previously requiring primary and secondary crushing for reintroduction into the production stream.
The high intensity mixing action produced by a Lancaster Mixer produces foam glass more efficiently than using a horizontal paddle style blender. This mixing process produces reduced process times and a higher quality mixture. The foam glass is typically used as a light weight aggregate in the building industry.
Call 1-800-447-7351 or Contact Us to talk to a Lancaster Products Representative about your glass granulation needs.
